1. Introduction
An Inventory Kit allows you to group several individual items together and manage them as a single product for sales, stock deduction, and fulfillment. For example, A “Gift Box” kit contains 1 Teddy Bear + 1 Mug + 1 Greeting Card. When sold, stock for all three items is deducted accordingly.
⚠️Important Note: You must have individual inventory items before creating a kit. If you have not created the inventory items, refer to How to Create Inventory Item. You can also perform Bulk Inventory Linking to add inventory items from the marketplaces.
2. Add Kit
Step 1: Navigate to Inventory on the sidebar menu > All Inventory Items.
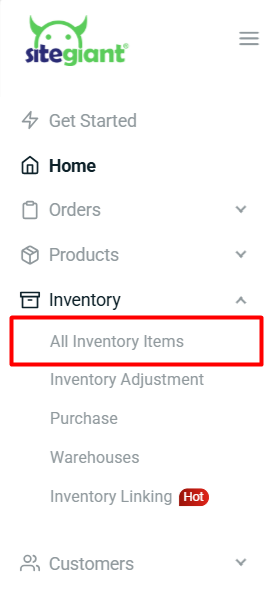
Step 2: Go to + Add New Item > Add Kit.
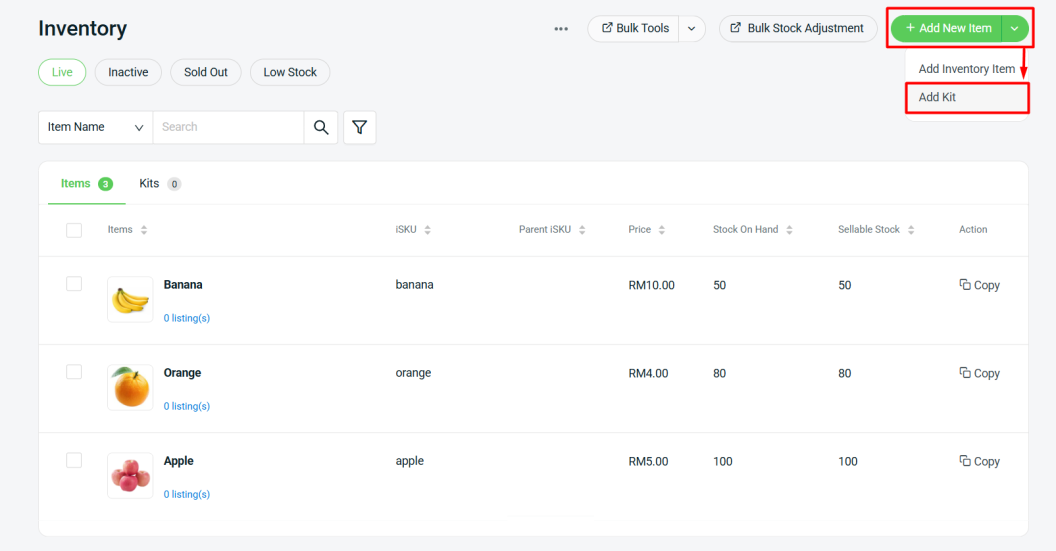
Step 3: Fill in the Kit Info accordingly.
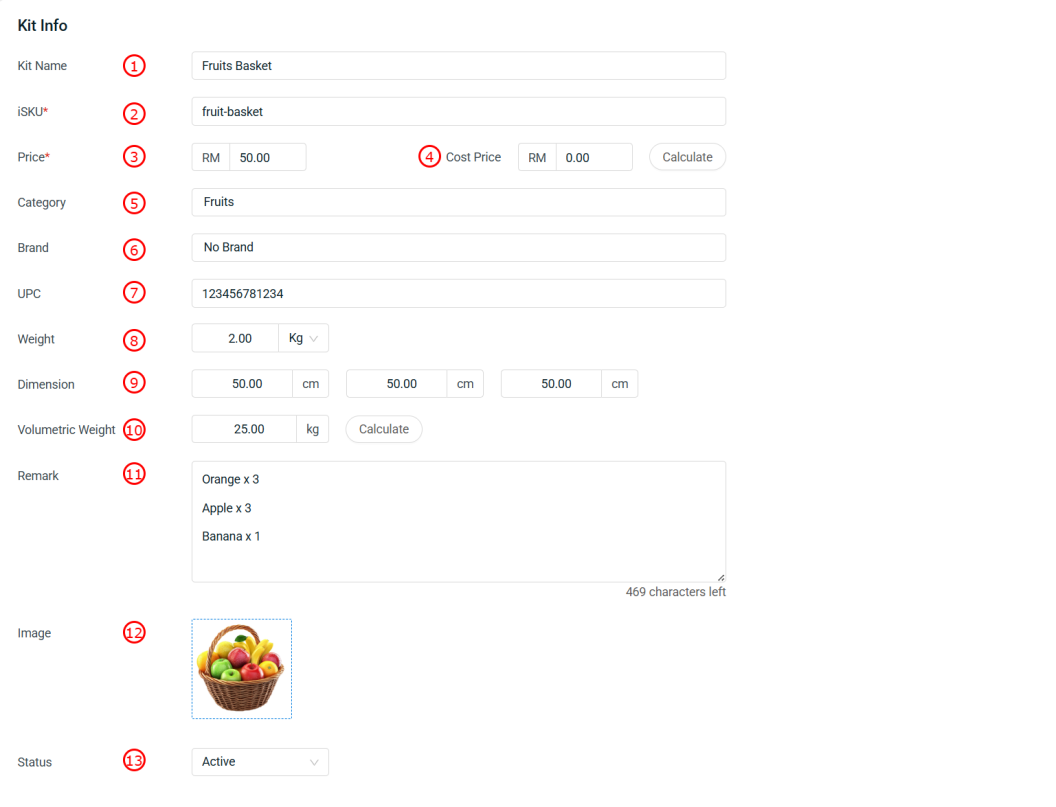
📌Note: Kit info with * is required to fill in. 1. Kit Name*: Name of the product or kit. 2. iSKU*:Inventory stock keeping unit (unique item code). 3. Price*: Selling price of the kit. 4. Cost Price: Purchase cost of the item. Click on Calculate after added the item list, system will automatically generate based on the cost of the items added. 5. Category: Kit category or classification. 6. Brand: Brand of the kit. 7. UPC: Universal Product Code, for barcode scanning. 8. Weight: Actual weight of the kit. 9. Dimension: Length, Width, Height of the kit. 10. Volumetric Weight: Shipping weight based on size, used for logistics. Click on Calculate, system will automatically generate the data based on the dimensions. 11. Remark: Additional notes or description of the kit. 12. Image: Upload the product image in JPG or PNG file. Recommended image size: 800 x 800 pixels and below 300KB. 13. Status: Allows you to change the status of a discontinued item to inactive. After changing the item status, you will no longer see it in the Live inventory item listing.
Step 4: Go to Item List tab > + Add Item > Select the item that make up this kit > adjust the Quantity if necessary.
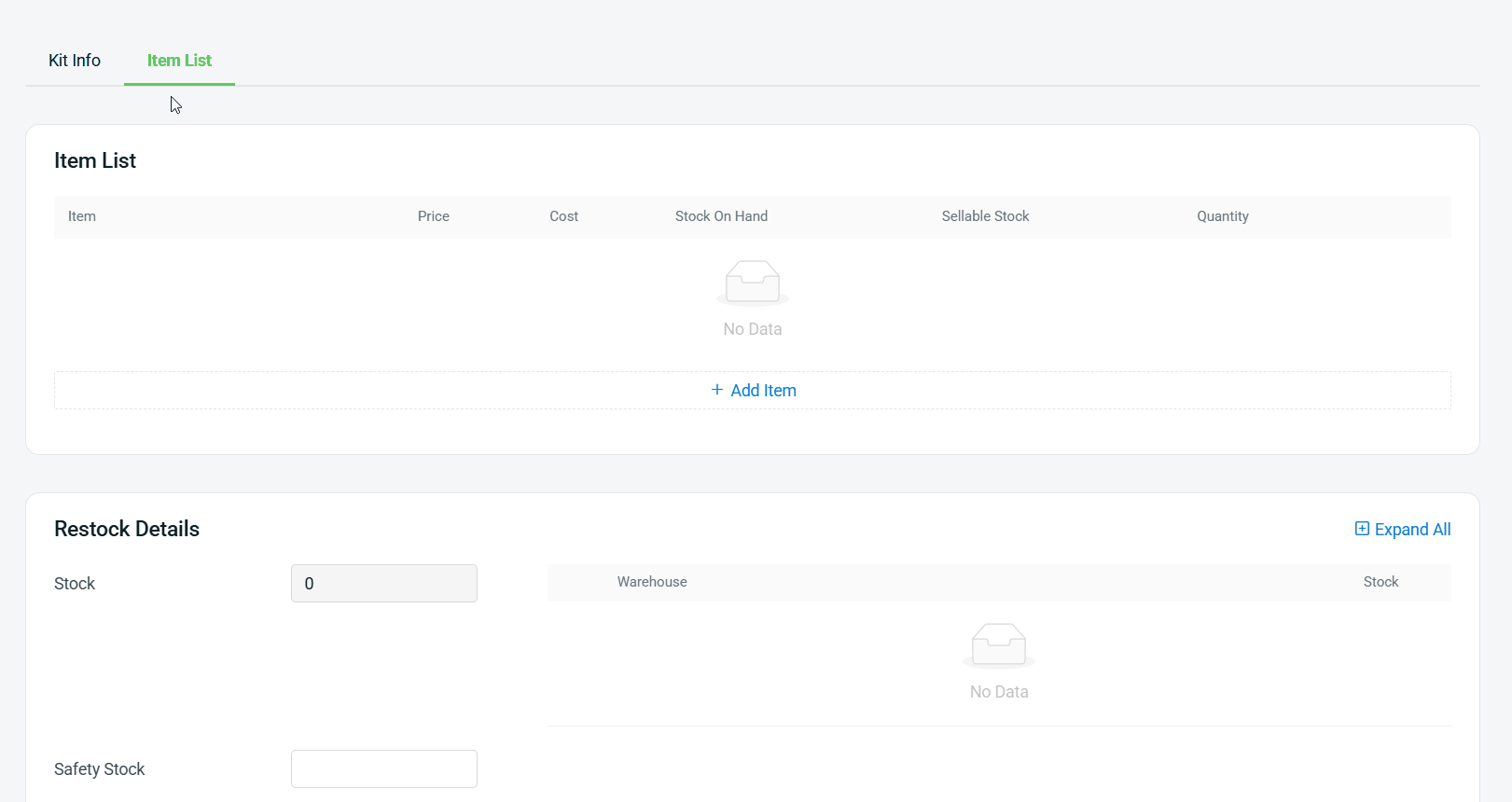
Step 5: Fill in the Restock Details accordingly.
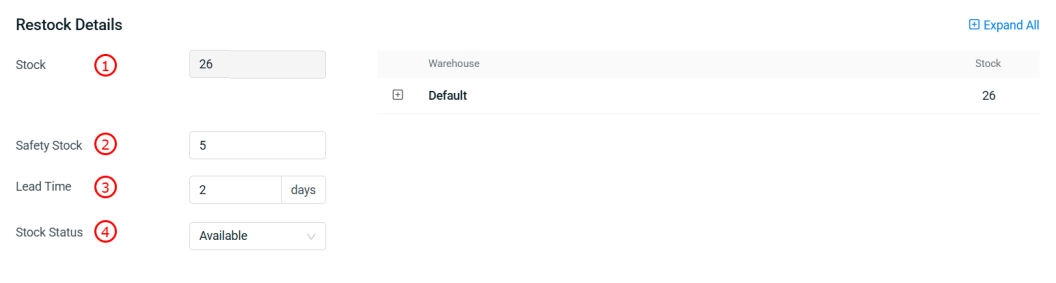
1. Stock: The stock of kit depends on the sellable stock of the selected items. The system will calculate how many stock can be assembled based on the lowest sellable stock among the included items. 2. Safety Stock: Minimum stock level for this item. When stock falls below this level, it will appear in Low Stock tab and may need restocking. 3. Lead Time: The number of days needed for the stock to arrive when restocking. 4. Stock Status: Controls how stock availability syncs to associated channel(s). By default is set as Available, stock syncs normally based on the sellable stock. If set to Out of Stock, system will force sync stock as 0 to associated channel(s), even if stock is available.
Step 6: Click + to expand the Warehouse column > click + Add Rack to assign the stock level to each rack.

💡Tips: Learn more on How To Manage Rack Group And Rack.
Step 7: Click Save to create kit.
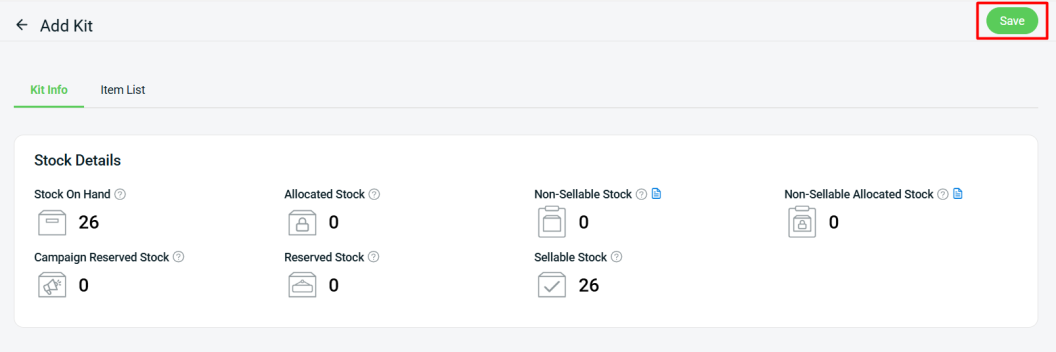